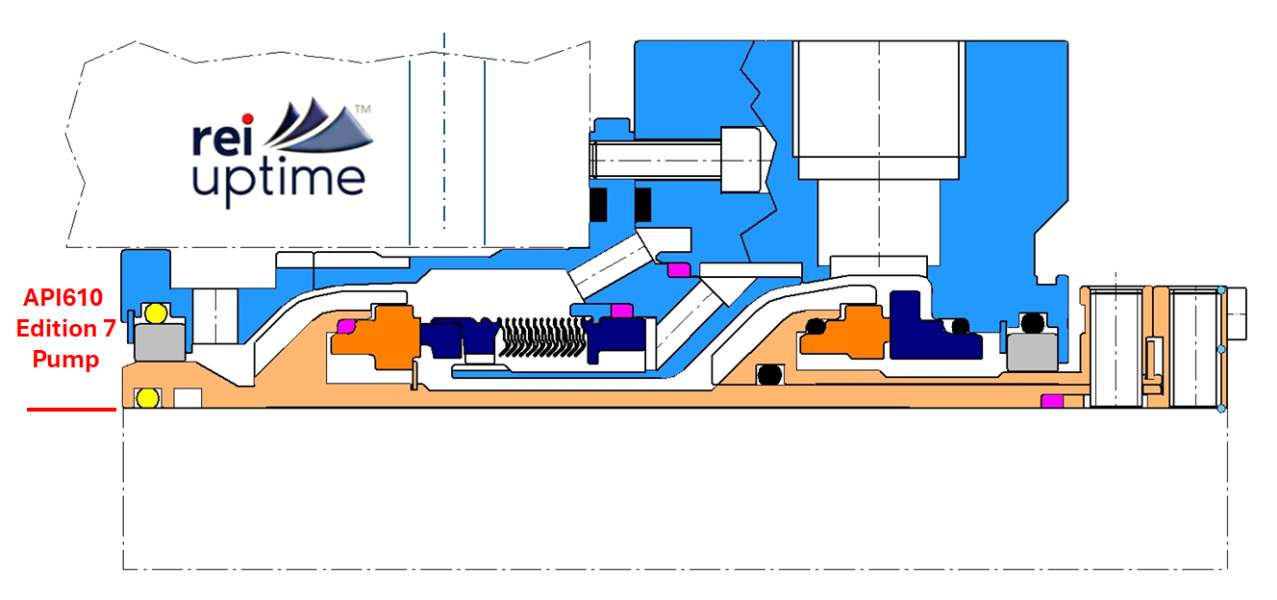
In life, good design can be appreciated no matter what the environment or context. Mechanical seal design is no different.
How many times do you experience the benefit of good product design? For example, when you fly on a plane and you sit on a well designed seat and immediately feel relaxed and comfortable. Yet on an alternate flight, with a different airline, the seat is hard plastic making the journey very unpleasant and uncomfortable. You end up getting out of the seat at the end of the flight with back ache, neck ache, and numb butt-cheeks or worse! ... Sciatica is not nice or health-enhancing!
You ask yourself, how is this possible when the physical leg room on the first flight was smaller?
There is something about the well-designed seat that enhances the customer experience and creates value-add to you. As a result, you are more likely to choose the airline with the better seat next time even if the price is a few dollars extra. This is because your health and wellbeing is THE most important aspect in the whole experience.
Good mechanical seal design follows the same principle as the aeroplane seat, no matter what pump environment it is placed in.
Let's take a traditional API610 Edition 7 centrifugal pump design. The standard was first published in February 1989 hence there are millions of these pumps in operation today across all industrial sectors and all applications.
The reader will note that the radial space between the shaft and seal chamber is significantly smaller in the Edition 7 pump design compared to later API 610 Edition 8 onwards. In light of a smaller seal chamber, some seal manufacturers switch off their 'best-practice' principles (as shown below) and default non-seal enhancing features, just like that plastic aeroplane seat designer! It doesn't have to be this way!
From the above seal design, the application is clearly hot as the design employs metal bellows seal faces. As there is no space in the API 610 Ed.7 seal chamber the seal designer has elected to implement a conventional, ineffective flush system rather than a Plan 23 design.
Furthermore, they have adopted a barrier fluid pumping scroll which has a VERY tight radial clearance between the rotating and stationary metallic members. That looks like a prime candidate for equipment seizure in a slightly out-of-align installation.
..... and, even worse, the barrier fluid is just circulated around the outboard seal faces .... in the hope that the inboard seal faces will 'fend-for-themselves'.
Overall, the seal designer has compromised on best-practice design techniques. They have thrown away Seal Reliability on the basis that it's an old pump and they can't fit anything else in the physical space...... WRONG!
No lets examine an alternate seal design, shown below.
The reader will note that its the same API610 Ed.7 pump environment yet the above seal design incorporates the highly effective Plan 23 system to cool the seal faces to about 30% of the process fluid temperature.
In addition, the seal incorporates a directed barrier fluid Plan 52/53 system, ensuring cooling media is circulated to both inboard and outboard seal faces..... AND, just when you think the seal design couldn't get much better, look at the radial gap between the rotating and stationary metallic members. No compromise there - fully compliant to the best practice principles of API682.
Good design principles do not need to be abandoned just because the pump is old, or the radial space isn't to the latest pump standards.
Equipment reliability starts at "good design". Sure, good manufacturing and inspection, and installation all help, BUT if the base point ... the aeroplane seat foundation is incorrect and unsuitable, then you can have the best plane engine and the best captain but you will still end up with an aching back and neck!
Want to read more about best practice rotating equipment design. Contact us and subscribe to our Continuous Personal Development classes and training.