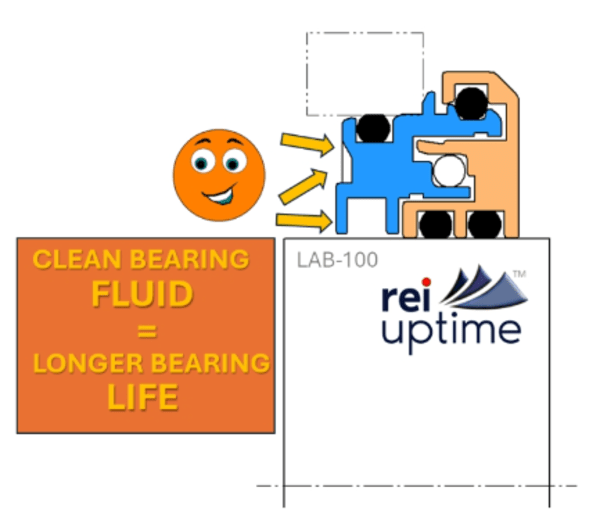
Bearing seals are critical in ensuring the longevity and smooth operation of rotating equipment. These seals act as a protective barrier, preventing contaminants from entering the bearing chamber while keeping lubricants intact. Whether you're working with motors, steam turbines, or spherical roller bearings, the right bearing seal can significantly enhance equipment reliability and performance.
In this comprehensive guide, we will explore what bearing seals are, the different seal types available, how to identify them, and best practices for maintenance.
A bearing seal, also known as an oil seal, shaft seal, or rubber seal, is a sealing device installed around the rotating shaft of machinery. Its primary purpose is to prevent the ingress of contaminants like dust, dirt, water, and other debris into the bearing housing. By retaining lubricants and protecting the bearings, these seals help to prevent premature wear and failure, ensuring the longevity of the equipment.
Bearing seals are essential components across various industries, from automotive systems to heavy machinery, and play a vital role in preventing downtime and costly repairs. When properly maintained, they extend the lifespan of motors, steam turbines, and other rotating equipment, improving overall operational efficiency.
There are two primary types of bearing seals—contact seals and non-contact seals. Each type has its unique advantages and is suited for different operating conditions.
Contact seals—such as lip seals and oil seals—utilise direct contact between the sealing element and the shaft to create a barrier against contaminants. This category of seals is effective at preventing external elements from entering the bearing housing. However, because they rely on direct contact, contact seals can generate friction and heat over time, which may reduce their lifespan. They are often made from flexible materials like rubber, which provide excellent sealing but may wear down with heavy use.
Non-contact seals, such as labyrinth seals, rely on a different mechanism to keep contaminants at bay. Instead of direct contact, these seals create a tortuous path or series of barriers that contaminants must navigate, preventing them from reaching the bearing chamber. Because they do not touch the shaft, non-contact seals generate significantly less friction, which makes them ideal for high-speed applications. In addition, these seals are typically more durable over time, thanks to reduced wear and tear.
Identifying a bearing seal can be done by examining its design, materials, and installation. For instance, contact seals often feature a flexible lip or rubber-like material that maintains direct contact with the shaft. On the other hand, non-contact seals typically have intricate labyrinth patterns or barriers designed to obstruct contaminants without touching the shaft.
When inspecting machinery, you’ll find that bearing seals are located at the ends of the bearing housing, surrounding the shaft. Knowing which seal type is used is essential for maintenance and replacement because each type of seal behaves differently under various operating conditions.
If you are working with specialised equipment such as spherical roller bearings or ball bearings, it's crucial to match the seal type to the bearing system. The right seal ensures optimal performance and longevity.
Routine inspection of bearing seals is critical to ensuring they are functioning correctly. During maintenance checks, bearing seals should be examined for any signs of wear, damage, or leakage. For contact seals, look for cracks, tears, or loss of flexibility. These types of wear can compromise the seal's ability to protect the bearing housing.
For non-contact seals, like labyrinth seals, debris buildup or contamination within the labyrinth passages can reduce their effectiveness. Over time, contaminants may breach the barriers, leading to damage inside the bearing chamber. It's also essential to check the alignment and lubrication levels to ensure smooth operation.
If you notice any signs of wear or degradation, it’s critical to replace the seals promptly to avoid further damage to your equipment. The right maintenance routine can significantly reduce downtime and extend the operational life of your machinery.
The choice of the best bearing seal depends on the specific operating conditions and requirements of your equipment. For applications where minimal friction and high speed are essential, non-contact seals like labyrinth seals are highly effective. These seals offer superior protection without generating excessive heat or friction, making them suitable for high-speed machinery.
However, in environments where contamination is more likely or where sealing must be tight, contact seals may be a better option. Rubber seals or grease seals work well in applications that require high sealing performance, particularly in industries where dust and water ingress are significant concerns.
For those working with spherical roller bearings or ball bearings, selecting the right seal type is crucial for ensuring smooth operation and equipment longevity. You may also want to consider seals specifically designed for harsh environments, such as those used in steam turbines or motors that are exposed to challenging conditions.
The LAB-100 is one of the most advanced labyrinth seals on the market today, designed for small cross-sectional spaces in rotating equipment bearing chambers. This premium seal offers superior protection and performance in even the most demanding environments.
Key Features of the LAB-100 Include:
Whether you are looking for improved equipment reliability or enhanced protection against contaminants, the LAB-100 labyrinth seal is an excellent choice for your sealing needs.
While labyrinth seals are ideal for many applications, you might also consider other options such as grease seals, which are effective at retaining lubricants in lower-pressure systems. In addition, rubber seals and ball bearings work well in applications that require high sealing efficiency. Be sure to select the right seal type based on your specific operational requirements.
Choosing the right bearing seals is crucial for ensuring the performance and longevity of your equipment. Whether you opt for contact seals or non-contact seals, regular maintenance and inspection are key to preventing equipment failure. To learn more about how our premium sealing devices can improve your machinery’s performance, explore the LAB-100 or contact us for personalised advice.